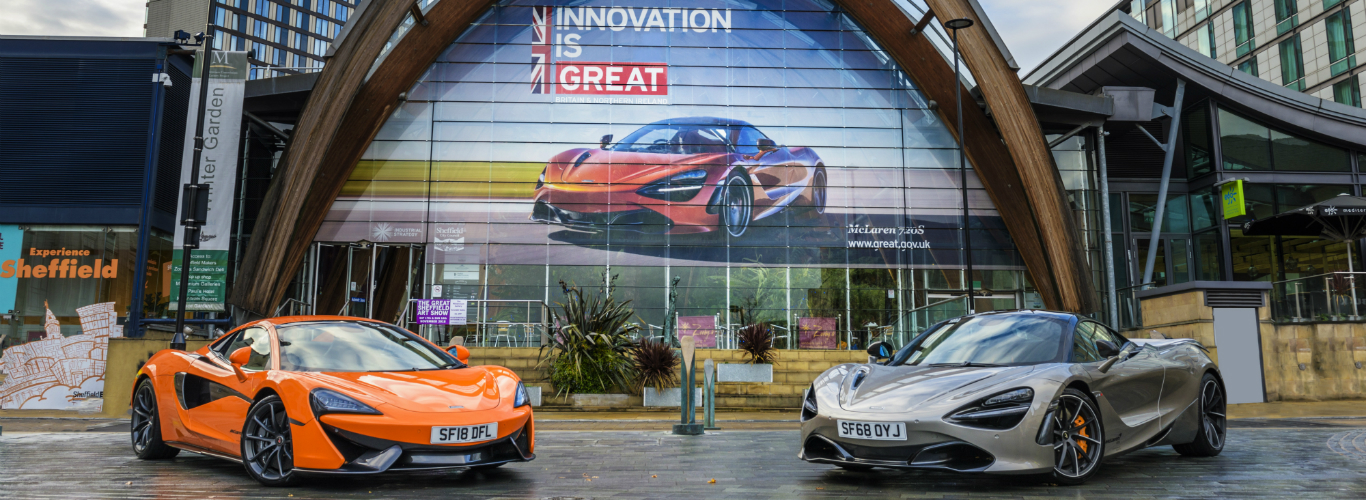
AUTOMOTIVE
South Yorkshire’s expertise in composites and light-weighting was a crucial factor in persuading the sports and super car brand, McLaren, to locate the development and manufacture of its advanced carbon fibre lightweight chassis on a purpose built, £50 million facility in Rotherham.
The AMRC has pioneered an advanced High-Pressure Resin Transfer Moulding system, which cuts cure times to just three minutes that supported McLaren Composite’s decision to locate here.
“At the AMRC we will have access to some of the world’s finest composites and research capabilities, and I look forward to building a world-class facility and talented team at the new McLaren Composites Technology Centre.”
Mike Flewitt, CEO of McLaren Automotive.
The AMRC, part of the UK's High Value Manufacturing Catapult, has become the model for collaborative research to transform the UK’s capacity for innovation and help drive economic growth.
AMRC counts amongst its clients leading manufacturers such as Bentley, Ricardo, Jaguar Land Rover, Runflat Systems, Nissan and TMG – Toyota Motorsport.
The AMRC is expanding its research activity into the next generation of electric vehicles with a strong focus on the smart manufacturing assembly processes that will be required to safely and efficiently build battery-powered drive trains and other key components of a cleaner, greener alternative to the internal combustion engine.
For further details or to discuss the potential for investment and partnership opportunities please phone +44(0)114 220 3444 or use our contact form to talk directly with our sector specialist.